Case07 持続的成長に向け、「カイゼンの企業文化創造」の実現を目指す
児玉化学工業株式会社 様
70年以上の長きにわたる歴史を持つ、プラスチック製品の老舗メーカー児玉化学工業株式会社。 乗用車やトラック・建機などの内外装部品から住宅設備・IT機器・アミューズメント領域に至るまで、多岐にわたる業界をカバーする総合OEMメーカーです。
プラスチックの可能性を追求し、「品質」を何よりも重んじる同社がDX化のパートナーとして選定したのがKMCでした。 KMCの「Σ軍師」導入によって得られた設備の見える化とその効果について、同社品質保証部の山根卓也部長にお話を伺いました。
■導入の背景 「文化を変えたい――」。 当社がDXソリューションの導入を決めたのは、社長のこのひと言からでした。 2020年に経営層が一新した際、企業成長の第1条件として『品質』がキーワードに掲げられました。そして同タイミングで当社のDX化に向けた取り組みが始まりましたが、当初は社員をはじめ幹部のほとんどがDX化には懐疑的でした。社内にも「IoT? M2M?」「思想はわかるけど使えるの?」「誰がやるの?」「今はまだ早いんじゃないか?」といったネガティブな意見で溢れていました。プロジェクトの担当者である私自身も過去に扱ったことが無い仕組みだったこともあり、当社のDX化は半信半疑でスタートしました。 そうした雰囲気の中で、KMC社の初回コンサルが始まりました。 すると、コンサルの過程で、工場内に散在していた品質・稼働状況・故障履歴などの様々な情報が分析され、以前から何となく気づいていた当社の課題が具体的に数値化されていきました。 結果として、KMC社からは以下5つの課題が提示されました。 1.データを正しくとる 2.不良を削減する 3.金型・設備の予防保全 4.得意とする既存工法の最新化 5.カイゼンの企業文化創造 これら5つの項目は、当社の誰もが「できていない」と気づきながらも、手を付けられていなかったことです。 KMC社のコンサルで数値化され改めて指摘されたことで、「何とかしなくては。これが“文化を変えたい”への答えとなる」と確信し、本プロジェクトが本格的にスタートいたしました。 とはいえ、答えの見えない、手探りでの改善の始まりであることは変わりません。 そこで、まずは「理解者を集める」「現状をしっかり把握する」ことから始めました。
■取り組み内容 実際の改善を進めるにあたっては、KMC社のコンサルで提示された5つの課題のうち、まずは「不良を削減する。機械稼動率を向上させる」「金型・設備の予防保全」をターゲットとして、DX化のスモールスタートを開始しました。 対象設備は「3,000tの射出成形機」としました。 本設備には以下のような特徴があり、当社のだれもが不良率低減・稼働率向上をあきらめていた機械です。 ・小ロット製品(30個~50個/1ロット)が多い・・・置き場も少ないため在庫が置けない。 ・1日の型替え/色替え回数が多い・・・自動車部品がメインのため、型替え回数は1日平均7回~10回。型替えでのロスが増える。 ・設備の老朽化・・・18年ほど使用している機械のため修理が多い。 「不良率が高く、稼動率が低いのは仕方がない」と、今まで手を付けてこなかった本設備を最初の機種に選定し、DX化に着手しました。改善前における同機の不良率は7%前後、設備稼働率は60%台と決して褒められたものではありませんでした。 まずは現状から見て、ロットを増やすには限界があると判断し、不良率ではなく不良個数を限りなく減らすことに拘ることとしました。 機械の稼動率についても「どこかに無駄な作業や動作があるはず。それを無くす」ということがテーマになっております。 DX導入への取り組みとして最初に着手したのはプロジェクト化です。過去の経験から、プロジェクトに必要な要素は以下の3つと考えています。 1.様々な部門から人選し大部屋化する 2.可能な限り若い人材を集める(新しいものへの抵抗感が無い人材の投与) 3.通常業務の内容にとらわれない組み合わせとする(既成概念にとらわれない創造力) この3つの要素で人材を集め、プロジェクト化することでまさに「文化を変える」ことが可能となりました。 製造現場の改善となると「製造部」が主体となるケースが多いかと思いますが、当社では様々な部署から選抜を行いました。なお、メンバーは部長や課長といった管理職ではなく、実務に携わっている各部署の中堅社員と一部新人で構成されています。
■導入の効果 活動開始時に掲げた目標である不良率3%以下(50%以上減少)を、4月以降で継続クリアすることができました(図1)。 途中、設備故障等で指標上は想定していた効果を出せてはいないものの、「Σ軍師」のデータから設備が治れば目標達成できることは予測ができております。
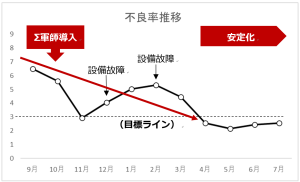
また、データから導き出された結果により、クッション位置のバラつきに着目しバルブタイミングを見直した結果、バラつきを大きく抑えることができました(図2)。この他にもバックフロー対策としてチェックリングの研磨を実施することにより、ショート発生率は対策前の1.8%から0.4%に大きく改善しています(図3)。
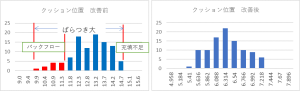
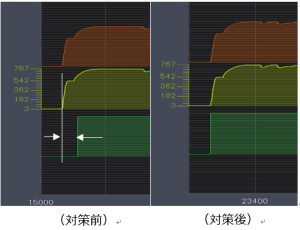
さらに、思わぬ効果も得られました。 「Σ軍師」のデータ解析による不良要因の発見や設備以外に起因する不良要因の数値化など、科学的なデータによる不良解析だけでは目標達成は不可能でしたが、改善活動を通じて製造現場に以下の新しい効果をもたらしました。 1.自分たちでできることを積極的に実施 2.今まで見ていなかった、日々の不良を意識したデータの確認 3.設備の不調や条件のアンマッチの確認、および金型清掃や点検の改良 例として、現場担当者が徹底的に機械を掃除したり、段取り担当者全員で型替えの動画を見ながらディスカッションすることで無駄な作業を極限まで減らすことができました。その結果、改善前で約40分かかっていた打ち終わりから打ち出しまでの時間が目標であった15分を切り、機械稼動率も80%台に改善しております。
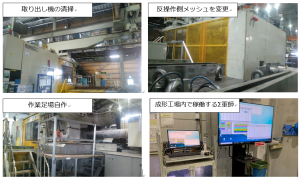
現場レベルでできることを自主的に始めるようになったということは、本プロジェクト最大の目標である「カイゼンの企業文化創造」へ向かって徐々に前進していると実感できています。このことは本プロジェクトにとって最大の効果であり、不良率や稼働率を上げることよりも今後大きな成果につながることと期待しております。
■今後の展望 現状では1台の射出成形機をDX化していますが、まだまだデータも少ない状況です。 当社が目指す生産プロセスの監視と計測、さらにその情報から設備や金型の予防保全につなげ、不良が出る前に対策を講じるというゴールにはまだ遠いと感じています。
不良数や事象、さらにその時の設備の状態や生産状況など、様々なことをデータ化して可視化する――。このことで新たな気付きが得られ、愚直に改善する人材が育って初めて大きな成果につながります。 DXはそのための1つの優れた道具です。 良い道具も使う側次第で錆びてしまいます。道具を活かすのは使う人材であり、道具と人材はセットで改善してゆく必要があると考えております。
※本内容は、「プラスチックスエージ」2021年11月号に講演された内容を一部抜粋して掲載しております。詳細資料資料につきましては、こちらよりダウンロードいただけます。
【商 号】児玉化学工業株式会社 www.kodama-chemical.co.jp 【所 在 地】東京都千代田区神田須田町2-25-16 日宝秋葉原ビル6階 【設 立】1946(昭和21)年3月 【資 本 金】1億円 【事業内容】プラスチック製品の製造販売